More a nd more pharmaceutical products are being produced i n ever smaller batch sizes and with short lead tim es: As a result, the entire supply chain i n the pharmaceutical industry is becoming increasingly complex.
For one of the world's leading manufacturers, t his led to serious bottlenecks in production. Even the p rocurement of the required folding boxes, labels and leaflets was unnecessarily complex and time-consuming. Faller Packaging helped the company make this pr ocess faster, more reliable, more cost-effective and more sustainable.
The customer is a global leader in the pharmaceutical industry, with a large packaging plant in southern Germany.
The increasing demand for its products caused the production volume at the manufacturer’s site to grow steadily year after year – but the on-site capacities could not be expanded to match the demand. More and more product variants with small batch sizes and short lead times led to bottlenecks in production, caused unnecessary costs and severely restricted the manufacturer’s delivery reliability and ability.
In the past, the pharmaceutical company had always relied on Faller Packaging for the procurement of its secondary packaging materials. The p ackaging specialist company constantly supplied folding cartons, labels and leaflets from one single source to the southern German production site. However, the customer always submitted a separate order for each product. A labour-intensive and unnecessarily compli-cated process.
In addition, the pharmaceutical manufacturer had to subject all incoming goods to a strict quality inspection - including the packaging components. However, the area where the deliveries to be checked were temporarily stored was limited and regularly overfilled. Errors in allocation and expensive delays due to overloading of the inspection department were the result. The company was not able to take advantage of the lower logistical and administrative costs that come with a system supplier. Instead, the processes for ordering, receiving the goods and releasing them became increasingly time-consuming and difficult to manage.
Together with Faller Packaging, the customer initiated procedures to make the procurement process simpler, more efficient and faster. The orders for folding cartons, labels and package inserts were bundled by product, and one order with several items for all secondary packaging materials was generated for each finished product. This allowed Faller Packaging to optimally distribute the items among its internal manufacturing capacities, produce them, and palletise them by product before shipping.
As part of a vendor-managed inventory (VMI) process, Faller Packaging also assumed complete responsibility for its products’ inventories at the customer’s site, enabling the pharmaceutical company to plan for raw materials and capacities at an early stage and to use them efficiently. In its role as a certified supplier, Faller Packaging also took over the inspection of the supplied products, thereby optimising the quality assurance process, since the pharmaceutical manufacturer no longer needed to conduct new in-house tests.
Benefits for the customer
- Time and cost savings through just-in-time delivery of the packaging materials to the packaging line
- Reduction of lead times in production by approx. 65%
- Reduction of expenses by around 400,000 euros
- Sustainable production through savings of several tonnes of set-up material
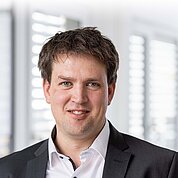